How to Test a Thermoactuator?
Updated on May 26, 2023
In every manufacturing facility, product testing is crucial to maintain high-quality standards. Thermoactuators are no exception. In this article, we will delve into the reasons behind testing our thermoactuators and provide insights into the testing processes we employ in our facilities. By explaining why and how we conduct these tests, we aim to ensure that our thermoactuators meet the highest standards of quality and performance.
If you're looking to have a better understanding of thermoactuators and their functions, we recommend checking out our informative blog post first.
Why Test Each Finished Product Before Delivery?
The significance of product testing during the production phase is widely recognized. However, in our case, conducting tests exclusively on semi-finished products is futile and insufficient. To ensure the highest quality standards, we emphasize the importance of conducting comprehensive tests on each finished product.
Here are some specific reasons why we perform thorough tests on each finished product:
- The wax motor, which is the core component of the thermoactuator, undergoes precision processing, including the use of tiny sealing rings. Even slight deviations during processing can impact its performance.
- The melting of wax inside the chamber generates high pressure (approximately 350 bar at a 70N load). It is crucial to ensure solid sealing to withstand this pressure.
- Testing allows us to verify the quality and performance of the working stroke, ensuring its compliance with our standards.
- Ensuring the electrical safety of the finished product is crucial as poor contact between the PTC thermistor and wax motor can lead to thermoactuator malfunctions.
Inspections on Raw Materials
The wax motor, being a small and intricately manufactured component, cannot be verified for quality just by eyes. To ensure the highest standards, we employ a Visual Inspection Machine to thoroughly examine the dimensions of raw materials before accepting them.
In addition, we conduct a comprehensive long-term heat resistance test on each new batch of plastic parts, specifically focusing on the plastic plunger. As this component bears high forces, its reliability is paramount. During the test, the plunger undergoes a two-week aging process at 170°C. Following this, it is installed in a complete thermoactuator for functional testing.
3 Types of Tests We Are Doing For Thermoactuators
To ensure the high-quality performance of our thermoactuators, we conduct three types of tests on finished products:
- End-of-Line Test for Each Finished Thermoactuator
Our commitment to delivering high-quality thermoactuators is evident in our comprehensive testing process. Using specially designed testing fixtures, we thoroughly assess the performance of each finished thermoactuator.
During the test, the thermoactuator is subjected to a counterforce of 80N and undergoes multiple cycles of 120s ON and 180s OFF at 230V. The software integrated with the testing setup automatically measures the working strokes and plunger operating speed throughout the test cycles.
Any thermoactuators that do not meet the required stroke or working speed are promptly identified, marked, and subjected to further analysis. Additionally, as part of the test cycles, we apply 500V to each thermoactuator for 10 seconds to ensure the absence of poor contact in the PTC bonding.
This rigorous end-of-line test ensures that no defective thermoactuators go undetected, guaranteeing that only qualified and reliable thermoactuators leave our factory. Our commitment to excellence drives us to maintain the highest standards of quality and performance in every thermoactuator we produce.
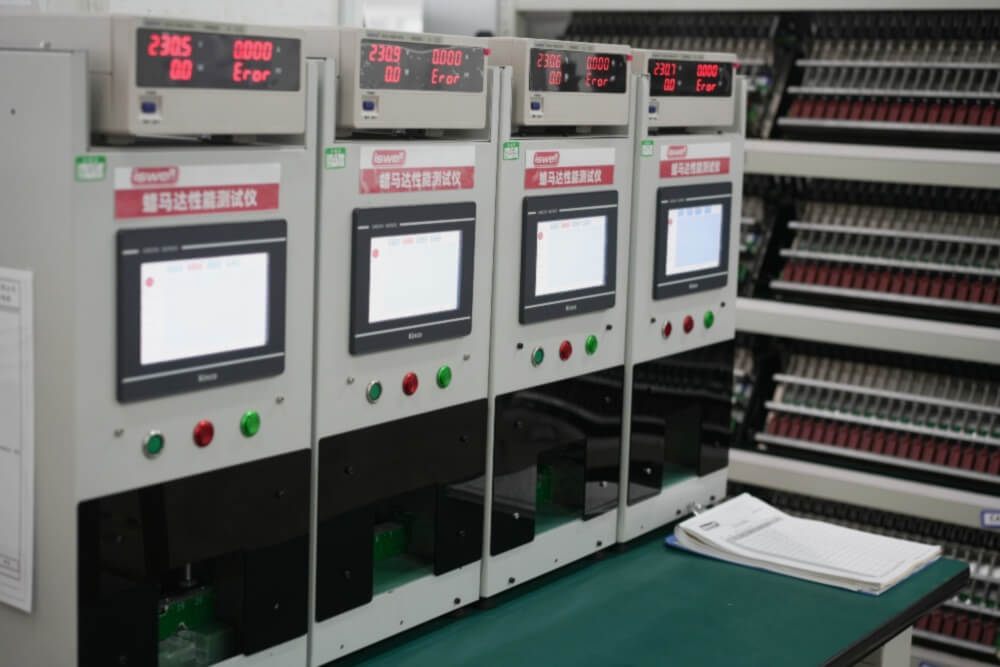
- Sampling Test
Following the rigorous end-of-line test process, we go a step further to ensure the quality and performance of our thermoactuators. We conduct additional verification by randomly selecting multiple thermoactuators for thorough evaluation.
To expedite the assessment and comparison of sample performance, we have developed Visualized Performance Test Machines. These machines incorporate visualized operating graphs, providing instant insights into the performance of the samples. This allows us to quickly assess and compare the performance of different thermoactuators, ensuring consistency and excellence in every unit.
- Life Cycle Test
The life cycle test is equally important as the stroke may attenuate over time with continuous usage under high counterforce. In this test, the thermoactuator undergoes cycles of 120s ON and 300s OFF, with a counterforce of 80N. The testing software includes an automatic cycle counter to keep track of the cycles. The test is considered successful when the number of cycles reaches 15,000 and the working stroke remains within the allowable range. This test ensures the durability and longevity of our thermoactuators.
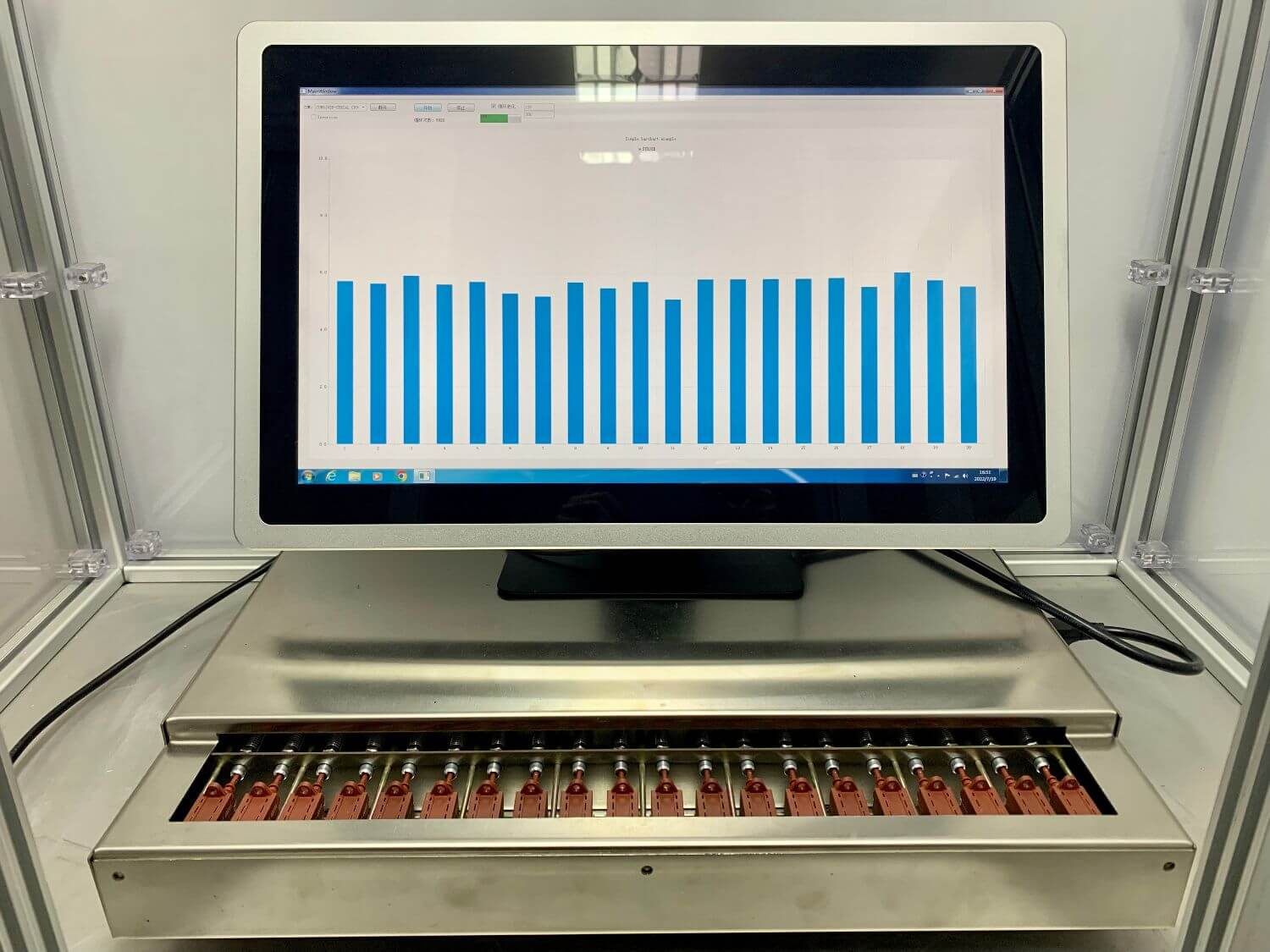
An outstanding thermoactuator surpasses mere qualification criteria. It must also exhibit exceptional long-term reliability, even when operating under high loads.
Bottom Line
Thorough testing of thermoactuators is essential to ensure high-quality standards and reliability. By conducting various tests, including end-of-line tests, sampling tests, and life cycle tests, we verify the performance, durability, and electrical safety of each finished product. Inspections on raw materials and comprehensive testing processes enable us to deliver thermoactuators that meet the highest standards of quality and performance. Our commitment to excellence drives us to continually improve and provide exceptional thermoactuators for various applications.